“十二五”期间,国民经济快速发展,特别是汽车产业、通讯产业的繁荣为压铸行业带来了极大的发展空间。这期间,工信部“重大技术装备自主创新指导目录(2012年版)”推动了压铸行业的整体自动化水平的提升。
2017年,我国有色金属压铸行业进入了一个崭新的发展时代。随着“中国制造2025”和“国家十三五规划”的发布实施,智能制造,创新驱动和信息智联已经成为传统制造业所面临的重大课题。目前我国压铸行业的生产水平普遍处在半自动化和自动化的水平, 压铸生产是高效率的生产方式,是现代制造方式之一,要充分发挥压铸生产的优势,必须实现产业升级,从自动化生产水平向数字化、智能化生产水平迈进。
压铸生产作为高效率的生产方式,一方面要保证生产的高效,另一方面要保证生产效率和产品品质的稳定,这就对生产过程中各个生产要素进行管理和监控,以及这些信息进行互联和共享。
压铸生产数字化是指从产品的模具设计、原材料供应、生产监控、质量监控、产成品库房管理等各个方面实现数字化,并把这些数字化信息实现互联和共享。各个方面产生的信息汇聚到生产管理系统中,生产管理中心再根据这些实时数据掌握生产状况,高效合理地调度和安排生产。准确的满足客户的订单需求,最终实现公司运营的高效益和高效率。
压铸生产数字化如果扩大到公司的供应商管理、客户管理,就能实现产品全寿命周期管理(PLM)。再进一步延伸到成本管理和库房管理,与公司的ERP系统对接就能实现公司的数字化运营管理。
1压铸生产过程
压铸生产包括原材料、模具、压铸现场工艺、品质检验等四个方面。其中品质检验贯穿其他三个方面。如图1所示。
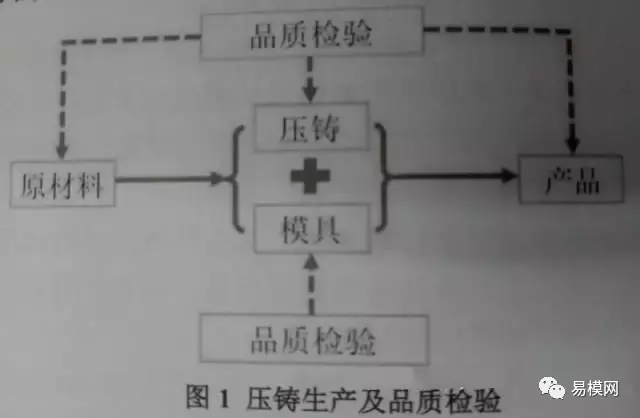
原材料方面:包括原材料的成分、机械性能要求。根据客户的材料要求和特殊性特性,提供符合要求的原材料。对原材料的检测项目要求主要有光谱分析、拉力试验、K值K模杂质检测和含气量检测等方面。
模具方面:根据客户提供的产品图纸和压铸生产要求设计压铸模具,利用UG或ProE软件进行三维模型设计,利用模流软件PROCAST进行压铸成型模拟,优化压铸模具的浇排系统和冷却系统,保证压铸生产时能够尺寸符合要求,内部质量符合要求以及连续稳定生产的要求。
压铸现场工艺方面:压铸现场工艺时压铸生产的最基本保证,它包括压铸参数、模具温度、铝液温度等直接工艺,还有设备运行状态、生产条件(水、电、气、液)等间接参数。压铸生产要求保证这些工艺参数的连续性和稳定性。
压铸参数主要指锁模力、压铸速度、增压压力、建压时间和料饼厚度等,这些参数来自于模具设计和模流分析,并在调试产品时的验证结果。压铸设计能够保证这些确定好的压铸参数在压铸生产时的稳定性,并且对这些参数能够进行实时监控,超出允差范围时发出警报信息。
模具温度是指压铸连续生产时为保证压铸件产品设计内部和表面质量而进行的控制,它同样来自于模具设计时进行的模具温度场的分析。模具温度的监控主要有点红外线和热成像仪两种方式,配置相应的监控仪器,实时跟踪模具关键部位的温度变化,进行记录以供工艺人员分析和调整,同时具有温度报警功能。
铝液温度是指铝液保温炉的温度监控,铝液温度是直接影响压铸产品的关键因素,铝液保温炉必须具有自动保持温度的功能,具有低温和超温报警功能。
设备运行状态主要是指压铸机和辅助设备的运行方式,包括自动、半自动和手动三种方式。
其他方面主要指冷却水的水压、压缩空气压力、电源和脱模液压力等基本生产保证因素。
品质检验方面:是指在压铸生产时主要保证产品的首末件的尺寸检验,还有中间产品的表面和内部质量检测。
2压铸生产数字化
上面分析了压铸生产全过程的各个方面,压铸生产数字化就是要对压铸全过程各个要素实现实时的检测和控制,利用软件对这些要素的信息进行分析和判断,生成各种参数趋势图和管理报表,具有智能决策支持的功能。
现代工业的发展,特别是自动化的发展,为压铸生产数字化提供了实现的工业基础。现代压铸机已经进入了工控电脑时代,它具备了压铸工艺参数的实时记录和存储能力,也全面集成了辅助设备的运行信息,包括给汤机、取件机、喷雾机、模温机和真空机等辅助设备。压铸机与这些辅助设备最主要的通讯方式是Profibus。
压铸生产数字化另外一个重要的方面是各种数字化传感器的普遍应用,主要有压力、温度、位移、热成像仪以及视觉识别系统等等。这些传感器为实现数字化甚至智能化奠定了基础。
2.1压铸单元数字化
压铸生产过程的主要数据如下:
(1)原材料的数据:主要有原材料的成分检测报告,力学性能报告和K值报告;
(2)模具的数据:主要有模具的3D模型报告,模流分析报告模具准备报告;
(3)压铸工艺数据:压铸单元的生产状态,压铸参数,模具温度,铝液温度和水电气等基本生产保证参数;
(4)品质数据:产品的全尺寸检验报告,过程尺寸报告、过程表面质量报告和过程内部质量报告;
(5)生产管理数据:生产订单、物料准备报告和产品产出,生产订单和物料准备报告报告来自于公司ERP系统的生产计划,产品产出报告来自生产现场的条形码扫描系统;
2.2压铸数字单元的智能互联
基于上述数据的压铸生产单元就是一个数字化的基本压铸单元,实现整个压铸车间的数字化还需要建立这些压铸单元的智能互联,智能互联目前国内主要方式是DNC和MDC,DNC方式是“distributed numerical control”,即分布式数字控制,它可以通过一台服务器实现对所有数字压铸单元的双向并发通讯,具有远程通讯和强制上传等功能,MDC方式是“manufacturing data collection”,即制造数据采集,它能够实现一台服务器同时自动采集4096个数字单元,兼容压铸机,机器人和自动化生产线等。
DNC和MDC系统结构图如2

2.3数字化管理
在数字生产单元和智能互联建立的基础上,建立数字管理系统才能把数字化的功能发挥出来。
MES系统是数字化压铸生产的中心,MES是“manufacturing execution system”,即制造执行系统。MES系统是指位于上层的计划管理系统与底层的工业控制之间的面向车间层的管理信息系统,它为操作人员/管理人员提供计划的执行、跟踪以及所有资源(人、设备、物料、客户需求等)的当前状态。
它能够通过信息的传递对从订单下达到产品完成的整个生产过程进行优化管理。当工厂发生实时事件时,MES能对此及时做出反应、报告,并用当前的准确数据对它们进行知道和处理这种对状态变化的迅速响应使MES能够减少企业内部没有附加值的活动,有效地指导工厂的生产运作过程,从而使其既能提高工厂及时交货能力,改善物料的流通性能,又能提高生产回报率。MES还通过双向的直接通讯在企业内部和整个产品供应链中提供有关产品行为的关键任务信息。MES系统的主要作用有:
(1)优化企业生产制造管理模式,强化过程管理和控制,达到精细化管理目的。
(2)加强各生产部门的协同办公能力,提高工作效率、降低生产成本。
(3)提高生产数据统计分析的及时性、准确性、避免人为干扰,促使企业标准化。
(4)为企业的产品、中间产品、原材料等质量检验提供有效、规范的管理支持。
(5)实时掌控计划、调度、质量、工艺、装置运行等信息情况,使各相关部门及时发现问题和解决问题。
(6)最终可利用MES系统建立起规范的生产管理信息平台,使企业内部现场控制层与管理层之间的信息互联互通,以此提高企业核心竞争力。
MES系统的架构如图3。
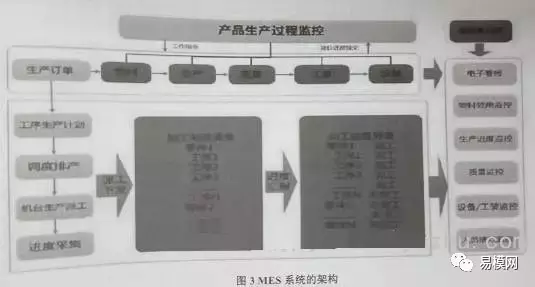
MES系统通过数字化排产、数字化生产协同、数字化资源管理、数字决策支持等方面的打造,可极大提升公司计划科学化、生产过程协同化、生产设备与信息化的深度融合,并通过基于大数据分析的决策支持对企业进行透明化、量化的管理,可极大提升生产效率与产品质量。
综上所述,压铸生产数字化使时代的潮流,是企业发展的需要,也是“中国制造”走上“中国智造”迈出数字化的脚步,为企业的发展,为中国智造作出努力和贡献!
|